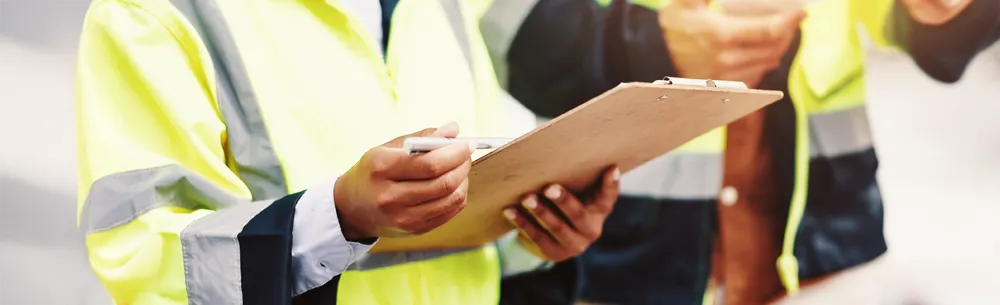
In these uncertain regulatory times, an OSHA violations list serves as a critical safety roadmap for contractors navigating potential changes in federal oversight.
The Occupational Safety and Health Administration (OSHA) has long been a cornerstone of workplace safety, even as its future remains in flux.
In 2023, the federal OSHA agency and state partners employed 1850 inspectors responsible for the health and safety of 130 million workers. This translates to about one compliance officer for every 70,000 workers.
It’s crucial to identify and address potential violations before they become serious problems – especially when regulatory support might be diminishing.
OSHA violations come in many forms from a contractor’s perspective. Each violation can have severe consequences, including:
- Direct financial impact from fines
- Project delays
- Increased insurance premiums
- Damage to reputation
- Criminal charges and incarceration
- Increased worker compensation costs
OSHA laws are subject to change as time goes on. No matter what kind of safety regulations exist, understanding critical workplace safety standards as well as the general OSHA inspection process is important.
While the future of OSHA might be in flux, contractors must remain vigilant about safety training protocols that protect worker well-being.
Key Takeaways About OSHA Violations Contractors Encounter
- OSHA violations can lead to severe consequences including fines, increased insurance premiums, criminal charges and higher worker compensation costs.
- Falls, slips and trips are the most prevalent OSHA cause of workplace deaths, with 38.4% of them in 2022 caused by this security issue.
- Common scaffolding accidents happen because of improper assembly, lack of cross-bracing and unsecured planking.
- Hazard communication security issues include failing to maintain Safety Data Sheets (SDS) for hazardous materials and inadequate worker training about chemical handling.
- Safety management software centralizes documentation, enables real-time hazard reporting and automates inspection scheduling.
Common OSHA Violations in Construction
Construction sites present many potential hazards, many of which have the potential to put workers at serious risk of physical harm or death.
Understanding the most common safety hazards that ended up becoming OSHA violations helps contractors and workers maintain safer worksites.
These violations persist partly because of tight schedules and budget constraints. But most of the time, they exist because people do not understand how serious the consequences of workplace hazards can be.
Each rule was put into place at some point because previous accidents and injuries demonstrated their necessity.
Failure to Implement Fall Protection
Construction workers often operate at dangerous heights. That is why fall protection is critical for worker safety.
Historically, the most prevalent OSHA violation involved failing to provide adequate fall protection systems. In 2022, 38.4% of construction workplace deaths were caused by falls, slips and trips.
Guidelines say that workers need protection when working 6 feet or more above the ground.

Failing to meet fall protection guidelines can lead to violations. Fall protection violations present themselves in many ways, including:
- Missing guardrails around open edges
- Lack of safety harnesses or safety nets
- Workers not wearing personal fall arrest systems.
Many contractors mistakenly believe workers can maintain balance without protection for “quick jobs.” This dangerous assumption leads to tragic accidents.
Even a fall from a low height can result in severe injuries or death.
This is why comprehensive fall protection remains crucial, regardless of if there is a federal law mandating compliance.
Incorrect Scaffolding Inspections
Scaffolding violations often stem from improper assembly and inspection procedures.
For example, erecting scaffolds without proper cross-bracing is an issue. So is the lack of secure planking or adequate guardrails.
When this happens, scaffolding becomes unstable platforms that can collapse.
Another common issue is failing to have a qualified person inspect scaffolding before each work shift.
Workers sometimes alter scaffolding without proper oversight, compromising its structural integrity. Load distribution problems on scaffolding mean that small modifications can create dangerous instability.
Ladder Safety Violations
While ladders might seem straightforward, their misuse leads to many citations and workplace injuries.
Common ladder accidents involved someone using them as work platforms instead of access points. Workers also often fail to keep three points of contact while climbing.
Workers often select ladders that are too short for the job, forcing them to stand on the top rungs or overreach.
Choosing the wrong-sized ladder can shift the user’s center of gravity. If it shifts outside the ladder’s base of support, it can lead to a serious fall hazard.
Additionally, damaged ladders often remain in service despite being visibly compromised.
Hazard Communication
Construction sites use many hazardous materials from solvents to concrete additives. Yet, proper hazard communication often falls short.
In 2020, around 174 construction injuries happened because of dangerous chemicals.
Historically, OSHA violations often involve failing to maintain Safety Data Sheets (SDS). Each hazardous chemical on the work site needs its own SDS. Technical violations also entail not training workers about the chemical hazards needed for the job.
Workers need to know the following for each potentially hazardous substance:
- Specific handling requirements
- Emergency procedures
- Personal protective equipment
Without proper labeling and employee training, workers may unknowingly expose themselves to dangerous chemicals.
Improper Respiratory Protection
Construction activities generate considerable dust, fumes and other airborne hazards. Such hazards make respiratory protection essential for workers’ well-being.
Common workplace safety hazards include things like:
- Not fit-testing respirators for individual workers
- Failing to check workplace conditions to determine appropriate respiratory protection levels.
Many contractors underestimate the long-term health effects of airborne particles. For example, silica dust from concrete cutting or welding fumes is toxic. Underestimating breathing hazards often lead to inadequate protection.
Medical evaluations to ensure workers can safely wear respirators are often overlooked. This oversight can put workers with underlying health conditions at risk.
Additional OSHA Violation Types
In addition to work-specific concerns, OSHA has also released a type list around the frequency and severity of the offenses.
1. Serious Violations
The hazard may create physical harm or cause death.
2. Other-Than-Serious Violations
Connected to the jobsite but wouldn’t lead to harm.
3. Willful Violations
An employer fails to comply with OSHA requirements or acts indifferently to employees’ well-being.
4. De Minimis Violations
Technical violations of OSHA expectations although there is no harm against employees’ health or safety.
5. Failure to Abate Violations
An employer doesn’t amend a previously cited violation by the OSHA deadline.
6. Repeated Violations
A business has not yet addressed a previously cited violation and receives another citation for the same offense.
The Best Way to Avoid Violations: Use Safety Software
Regardless of how strict the laws are regarding safety and compliance, safety management technology is a critical tool for contractors seeking to maintain a safe workplace.
While OSHA’s future role is uncertain, creating a culture of safety is important. That’s why safety software provides a robust solution for managing critical safety documentation.
Managing construction safety through paper-based systems creates unnecessary risk and administrative burdens.
Construction sites generate extensive safety documentation daily:
- Training records
- Equipment inspections
- Hazard assessments
- Incident reports
- Corrective actions
Without a centralized system, critical safety information gets lost. Safety issues develop. Worst of all, violations become more likely.
Modern safety management software transforms how contractors handle these challenges.
Digital platforms enable real-time hazard reporting, automated inspection scheduling and instant distribution of safety updates across jobsites.
By using software, workers can document safety meetings protection standards and equipment checks through mobile apps. Supervisors can track completion rates and identify trends through comprehensive dashboards.
Safety software can prevent violations before they occur. Contractors can maintain continuous compliance rather than scrambling to address issues during inspections.
Digital records meet current OSHA requirements while enabling quick retrieval during inspections.
This technology provides consistent documentation across all job sites for managing multiple projects. It ensures safety of employees remains a top priority – regardless of potential regulatory changes.
SafetyHQ® can help Contractors Manage Everything Safety
Proactive workplace safety is important regardless of if there are federal laws mandating compliance with safety standards. Even though OSHA’s future role may be uncertain, it is in a construction company’s best interest to prioritize worker protection.
The construction industry pose serious safety risks. Nearly 1 in 5 workplace deaths happened at construction jobsites.
Accidents resulting from safety issues can result in severe penalties for contractors.

The most common violations in the past included:
- Inadequate fall protection
- Improper scaffolding assembly
- Ladder misuse
- Insufficient hazard communication
- Inadequate respiratory protection
Managing safety compliance through paper-based systems creates unnecessary risks and administrative burdens. Safety software centralizes documentation, enables real-time hazard reporting and automates inspection scheduling.
SafetyHQ streamlines safety management by centralizing all safety processes in one digital platform. The mobile app enables real-time hazard assessments, equipment inspections and training documentation. Plus, safety managers can walk though the OSHA inspection process even before the inspector shows up.
The app tracks due dates, generates notifications and maintains comprehensive records. All these features meet OSHA documentation requirements.
Even though we can’t predict the future, proactive contractors can stay ahead of potential changes by maintaining comprehensive safety protocols to create a safe workplace.
For more information about the SafetyHQ construction safety app, speak with an expert today.
Share Article
Keep on current news in the construction industry. Subscribe to free eNews!